90.000
units, daily production potential
185
sqm of production plants
UNI
UNI EN 14683:2019
2
laboratories for testing
Diamant, based in Verona, manufactures and markets surgical masks of type IIR intended to be used both in healthcare and in other professional and social contexts. Production is carried out by automatic machines. The entire production process is planned, managed and controlled in accordance with the provisions of the Medical Devices Regulation (EU) 2017/745. Particular attention is paid to the quality control of production environments and to the traceability of the product throughout the production chain, from raw materials suppliers to the final customer.
Before starting the production cycle, a sample of facial masks is made, intended for the laboratory tests required by the reference standards. Tests that define the type of product and its intended use and ensure its biocompatibility. After a first phase of sampling, a second phase of testing is carried out to confirm the accuracy of the results, before starting production.
At the end of the laboratory tests, a technical documentation is drawn up to ensure that the product complies with the validated sample. All data are reported in the Product Data Sheet of the device. Later, the raw materials for production are ordered, controlled and stored in the warehouse and registered in the accounting warehouse management software.
The production line begins with the reception in the warehouse of the materials necessary for the production of the masks. After an accurate check, the raw materials are stored and recorded in the dedicated management software of the accounting warehouse. Subsequently, we move on to the cutting of fabrics in the laboratory and to the control of pre-cut rolls, also registered in the software, as semi-finished products.
Before being processed, all the materials used in the manufacture of facial masks are subjected to a sanitizing pretreatment inside an ozone sanitizing cabin. At this point we move on to the production and packaging process of the product which is fully automatic and includes various phases: Coupling and cutting of the fabric, pleating, cutting and insertion of the nose clip's underwired, thermowelding of the horizontal edges, cut of the single piece, application of the lateral elastic band, drawing and labeling.
Then follows the secondary packaging of the product in boxes of 50 pcs with its labelling.
The masks produced are subject to constant monitoring: with established frequency samples are taken along the entire production line to be subjected to visual checks related to welding of the edges and elastic bands, position of the nose clip and proper sealing of primary packaging. Moreover, random tests are carried out on the elastic traction to verify that it is always in line with the standard values.
For each new production batch, a microbial cleaning control is performed at an external laboratory by means of a Bioburden test.
The hazards related to the design phases, The manufacturing, use and marketing of Diamant Surgcal Face Mask devices have all been evaluated and led to the conclusion that the devices are safe in their declared use and the residual risks are acceptable.
In particular, the increased risks were addressed through design in accordance with the reference standards and appropriate identification and verification of the relevant performance characteristics, as regards functionality aspects, specificity and security.
Appropriate warnings relating to residual risks have been included on the product label and in the Instructions for use. In the after-sales phase, information on the product and any reports of non-compliance are monitored and collected . All information is managed using the procedures established in the Quality Management System and any corrective actions are recorded in order to account for the evolution of the risk management plan.
A complete traceability between producer and final customer is guaranteed thanks to a precise registration of raw materials, the products stored and finished in the management software and the digital storage of all the technical documentation of the product and the Transport Document (DDT). In addition, each movement of the raw material is recorded to have a precise evidence of storage per batch.
The technical file, prepared in accordance with the Medical Devices Regulation (EU) 2017/745, is the collection of all the documentation that illustrates the life of the product, from the moment of its conception and for all the successive phases of its life.
This documentation is constantly updated to keep track of any subsequent developments along the product life cycle.
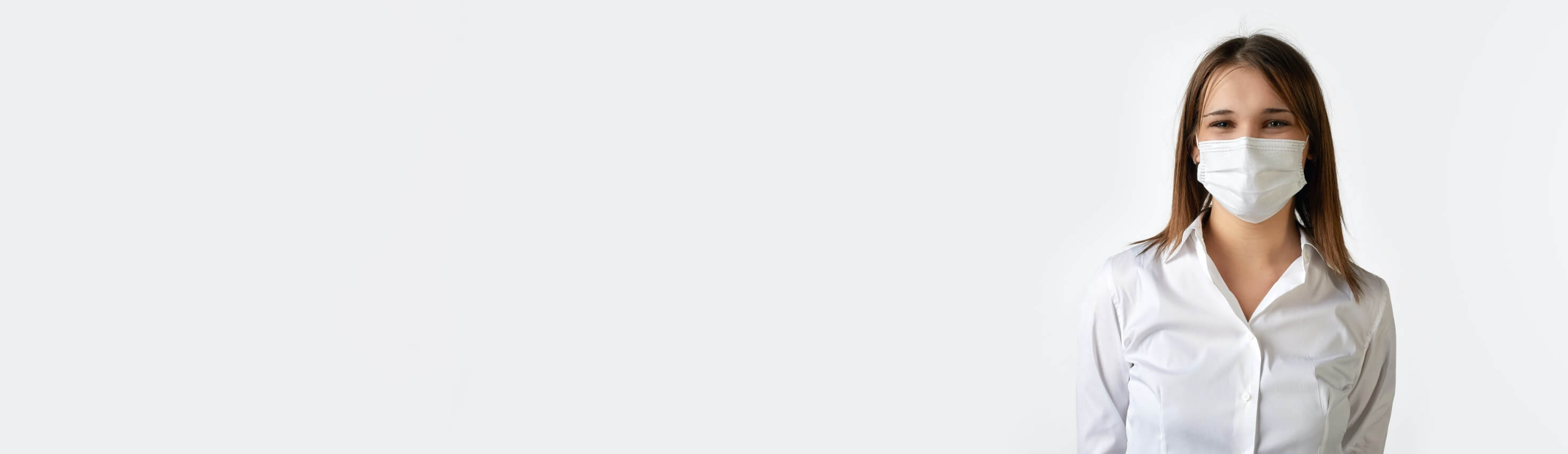
INFORMATION
Do you need assistance or contact the sales department?